- Innovation créatrice de nouvelles compétences
- Oui
- Innovation génératrice de nouvelles activités
- Oui
- Phase de développement de l'innovation
- Commercialisé depuis plusieurs années
- Date de création
- Date de mise à jour
En bref
L'aluminium est le métal le plus récemment découvert puisqu'il n'est entré dans sa phase industrielle que depuis la fin du XIXe siècle.
L'automobile a succombé très rapidement aux charmes de ce métal au départ très cher, vu son mode fabrication, et qui était réservé à l'orfèvrerie et à des utilisations dans le luxe.
C'est ainsi que l'on voit, en 1899, le belge Camille Jenatzy et la « Jamais Contente », voiture électrique à carrosserie en Partinium, alliage d'aluminium (Al + Tungstène + Magnésium laminé), battre le record des 100 km/h. Aujourd'hui, la voiture de monsieur tout le monde ne bat plus de record mais utilise toujours des alliages d'aluminium.
Dans le secteur automobile, la substitution de l'acier doux par l'aluminium a crû de façon constante au cours des cinquante dernières années. Durant cette période, la quantité d'aluminium dans une voiture est passée de moins de 40 kg à plus de 180 kg. D'abord introduit dans la fabrication d'élément mécanique, l'aluminium a progressivement fait son chemin jusqu'à la structure, sans oublier les éléments de carrosserie qui constitueront la plus forte croissance. Dans le futur, une voiture contiendra près d'un quart de son poids en aluminium, qui sera intégré dans un ensemble multi-matériaux.
- Innovation créatrice de nouvelles compétences
- Oui
- Innovation génératrice de nouvelles activités
- Oui
- Phase de développement de l'innovation
- Commercialisé depuis plusieurs années
- Date de création
- Date de mise à jour

Description détaillée
L'aluminium est un métal de couleur argentée. Cependant, il n'apparaît pas dans la nature à l'état métallique pur, mais est extrait à partir de minerais. Le plus important est la bauxite que l'on utilise pour la fabrication industrielle. Les gisements du minerai sont très nombreux et importants sur tout le globe. Les plus vieux, aujourd'hui épuisés, étaient dans le sud de la France, en particulier près du village des Baux-de-Provence, qui a donné son nom au minerai.
La bauxite est un mélange d'oxyde d'aluminium, l'alumine, d'oxyde de silicium, d'oxyde de fer, d'oxyde de titane et d'eau. Les teneurs de ces différents éléments sont variables selon les minerais :

La fabrication de l'aluminium se décompose donc en deux étapes :
- Extraction de l'alumine par attaque de la bauxite à température et pression élevées au moyen d'une solution de soude caustique (procédé Bayer). Les impuretés sont séparées de la solution par décantation et filtration. L'alumine se présente, alors, sous la forme d'une poudre blanche.
- Fabrication de l'aluminium par électrolyse de l'alumine, vu que l'aluminium forme avec l'oxygène une liaison chimique très stable et qu'il ne peut donc pas, comme dans le cas du fer ou du cuivre, être extrait par fusion.

La consommation électrique de l'électrolyse de l'aluminium est importante, de l'ordre de 13.000 kWh par tonne d'aluminium produite et la production d'aluminium engendre une forte pollution en rejetant des déchets qui doivent être stockés. De plus, elle nécessite une consommation importante en eau. Aujourd'hui, on utilise de plus en plus de l'aluminium usagé, si bien que les besoins d'extraction de la bauxite et la consommation d'énergie nécessaire à la production de l'aluminium se réduisent par rapport à autrefois, grâce au recyclage.

L'aluminium a de nombreux atouts qui ont très vite intéressé l'industrie automobile :
- C'est le métal le plus léger après le lithium et le magnésium.
- Il conduit bien l'électricité et la chaleur.
- Il n'est pas magnétisable.
- Il a une bonne résistance à la corrosion.
- C'est un métal robuste.
Malgré tout, la résistance mécanique de l'aluminium pur est relativement faible. Cette résistance mécanique peut être notablement augmentée par l'addition d'autres métaux, formant ainsi des alliages. Ceux-ci peuvent être classés en deux catégories :
- Les alliages sans durcissement structural (alliages non trempant),
- Les alliages à durcissement structural (alliages trempant).
Cette différence entre alliages est due à l'élément d'addition principal, cependant des additions d'éléments secondaires vont aussi influer sur les caractéristiques de l'alliage.
Les alliages d'aluminium sont classés en sept familles ou séries selon l'élément principal d'addition. Les alliages sont communément désignés par un numéro à 4 chiffres dont le premier désigne la série :
- Aluminium sans élément d'addition : 1000
- Aluminium + cuivre : 2000
- Aluminium + manganèse : 3000
- Aluminium + silicium (alliages de moulage) : 4000
- Aluminium + magnésium : 5000
- Aluminium + magnésium + silicium : 6000
- Aluminium + zinc + magnésium : 7000
Les éléments de carrosserie en aluminium sont généralement fabriqués d'alliages de la série 6xxx à traitement thermique après emboutissage, du moins pour les tôles extérieures.
La résistance à la déformation nécessite une limite d'élasticité suffisamment haute pour pouvoir résister aux déformations permanentes de ce fait, on choisit en général pour les ouvrants des alliages d'aluminium durcis par vieillissement.
Transformation et mise en forme
Une fois que l'aluminium a été extrait et transformé par addition des éléments d'alliage, il faut bien sûr lui donner sa forme définitive. La mise en forme s'exécute en deux temps. Tout d'abord, le matériau brut doit être laminé pour obtenir des tôles, en plusieurs étapes jusqu'à ce que l'épaisseur de tôle voulue soit atteinte. Ensuite, les tôles sont mises en forme selon les exigences par emboutissage.

En fonction du degré de déformation plastique de la pièce de carrosserie à produire, l'emboutissage s'effectue également en plusieurs étapes.
Mais après l'emboutissage, les éléments de carrosserie en aluminium sont encore trop tendres, c'est pourquoi leur rigidité doit être augmentée par durcissement structural (traitement thermique : chauffe et refroidissement). C'est aussi lors de ce traitement thermique que les éléments d'alliage établissent une liaison avec l'aluminium, déforment le réseau atomique et engendrent par là-même une plus grande rigidité.

Un élément de peau ou pièce d'aspect en aluminium se distingue par une rigidité extrêmement élevée et un poids nettement inférieur à l'acier. Ce qui se traduit par une réduction de la consommation en énergie et des émissions de carbone, plutôt dans l'air du temps. De plus, il assure une grande sécurité en cas de collision, une diminution des risques de corrosion et de l'impact environnemental.
Ce matériau répond aussi au problème de répartition des masses, il est devenu le matériau de référence pour la fabrication de nombreux ouvrants, comme le capot, les portes ou la malle arrière mais aussi certains éléments fixes, les ailes avant.

Les éléments en alu de la Volkswagen Lupo
Diffusion sur le marché | Pour les éléments de carrosserie, le coût actuel de la matière première et le développement d'acier plus léger ont tendance réserver ce matériau au véhicule à forte marge (haut de gamme |
---|---|
Constructeurs concernés | Tous les constructeurs. |
Innovation engendrant des entretiens | Non |
Innovation engendrant des réparations | Non |
Dispositif législatif en rapport avec l'innovation | Aluminium et alliages d'aluminium ; NF EN 487- Plaques de laminage. Instruction technique de l'OTC IT F6 |
Contrôle technique | Les éléments de carrosserie qui participent à la structure du véhicule ne doivent pas présenter de déformations ou de corrosions excessives. Si le risque de corrosion est relativement faible sur des organes en aluminium, les éventuelles réparations de chocs feront l'objet d'un examen soigné. La découverte d'une anomalie pouvant générer une défaillance majeure soumise à contre-visite, ou, dans les cas extrêmes une défaillance critique limitant l'utilisation du véhicule au jour même du contrôle. |
Mots-clés | Aluminium, alumine, bauxite |
Méthodes et pratiques
Un élément de carrosserie en aluminium ne nécessite pas d'entretien ou de réparation sans qu'il ne soit endommagée par un accident de la route. C'est ce que l'on appelle la réparation-collision.
Après l'analyse des dommages causés, la décision de réparer ou remplacer un élément de carrosserie peut être difficile à prendre. Avec l'aluminium, nous devons être conscients que certaines réparations ne peuvent se faire de la même façon que sur un élément de carrosserie en acier. Pour autant nous n'avons pas besoin d'abandonner toutes nos expériences passées pour nous aider à trouver les meilleures solutions.
La remise en forme d'un élément de carrosserie commence par une définition des moyens et des méthodes qui permettront de restituer les caractéristiques d'origine à l'ensemble du véhicule par le biais de cet élément.
Les critères de conformité (définis par le constructeur), sont l'esthétisme, le fonctionnement et la sécurité.
Si l'on ne peut pas satisfaire à ces critères, il faut songer à remplacer l'élément.
C'est en fonction du redressage à réaliser que l'on choisit une technique :
- "Élément déformé dont la face intérieure est accessible" : par planage/rétreinte avec des outils actifs/passifs prévus pour le travail de l'aluminium et rétreinte à chaud si nécessaire.
- "Élément déformé dont la face intérieure est non accessible" : par traction ou inertie avec un tire-clou spécifique aluminium.
Suivant l'accessibilité et l'ampleur de la déformation, le réparateur doit utiliser un type de matériel bien précis, seul ou en complémentarité.
Avant de commencer le redressage et pour réaliser un travail de qualité, il est préférable de gratter toutes les peintures et les insonorisants qui pourraient gêner l'opération.
Lors d'un redressage classique (marteau et tas), on utilise :
- Une force exercée sur le tas pour combattre l'élasticité de la pièce.
- Une force exercée au martelage du maillet ou de la batte.
La déformation étant localisée, il y aura création d'une crête d'arrêt.
Le métal y est particulièrement écroui, car au moment de la compression il a constitué une sorte de charnière.

Cette crête d'arrêt, formant parfois une arête très marquée, empêche le métal de reprendre sa forme, car c'est la zone où il y a eu création du maximum de tensions internes.
On devra tout d'abord situer les points de bridage, les crêtes d'arrêt et, s'il y a des sections plus rigides (renforts, doublures, etc.), il faudra commencer la réparation par ces sections car, du fait de leur résistance, elles empêcheront la tôle de reprendre sa forme initiale.
L'expérience montre que la plus grande partie de ces déformations, voire la totalité, disparaîtra dès que les points de bridage de la crête d'arrêt seront libérés.
Ensuite on réalise un sous-planage qui redonne à l'élément son profil initial et on finira par un planage qui assure la finition de l'état de surface du profil initial retrouvé.
Le martelage à bout portant a pour effet de diminuer l'épaisseur du métal, il gonfle, jusqu'à former une cloque. Cela peut être résorbé par une rétreinte à chaud (au chalumeau OA).
Durant le chauffage aucun changement de coloration n'est décelable sur l'aluminium. Il est donc indispensable d'utiliser des moyens de contrôle thermique (savon de Marseille, étiquette ou crayon thermique).

Le tire-clou ou spotter est utilisé pour restituer la forme générale de l'élément, lorsque l'accessibilité sur les faces internes de celui-ci est difficile ou impossible avec l'outillage actif/passif.
Le point de soudure est généré automatiquement par un simple contact entre l'outil et la pièce à redresser, sachant que nous avons au préalable fixé la masse sur le véhicule. Cet outil existe avec deux pinces de masse ou un tripode.
Le spotter soude des goujons filetés en aluminium munis d'une pointe d'amorçage pour favoriser l'ancrage du goujon.
Pour effectuer un redressage avec un spotter, il faut :
- Travailler sur une tôle décapée.
- Effectuer des essais de réglages sur tôle de même nature que celle à redresser.
- Positionner les masses de soudage de part et d'autre et à proximité de la zone à redresser de façon à concentrer l'énergie de soudage.
- Pour souder le clou, appuyez sur la gâchette du pistolet, exercer un contact franc, souder les clous dans l'ordre chronologique et perpendiculaires à la zone à redresser.
- Positionner l'appui sur un point dur, doublure ou renfort, et exercer une traction à l'aide du levier. Chauffer le pourtour du renfoncement, l'aluminium se travaille plus facilement à chaud.

Entreprises concernées aujourd'hui | Carrosserie / Peinture, MRA, RA2, RA1 |
---|---|
Métiers concernés | Carrossier et Peintre, Réceptionnaire |
Impact sur les compétences en atelier
- Connaître le matériau aluminium (propriétés, caractéristiques,...).
- Savoir utiliser des outils actifs/passifs pour aluminium.
- Savoir utiliser les différents outillages complémentaires (tire-clous, tringles de redressage,...).
- Savoir utiliser un chalumeau OA et les moyens de contrôle thermique (savon, étiquette thermique,...).
- Savoir souder l'aluminium (soudure MIG).
- Savoir remplacer un amovible en aluminium.
- Savoir effectuer les traitements de surface sur aluminium (ponçage, recharge de matière, impression époxy,...).
Exemple d’outillage approprié
Certains constructeurs (dont Peugeot et Renault) ont développé une gamme d'outillage actif/passif spécifique en matériaux composites avec une âme métallique.

Tire-clous aluminium (spotter) avec les goujons soudables en aluminium munis d'une pointe d'amorçage de diamètre 4 à 6 mm (disponible chez tous les fabricants de poste à souder).

À lire aussi dans la même section
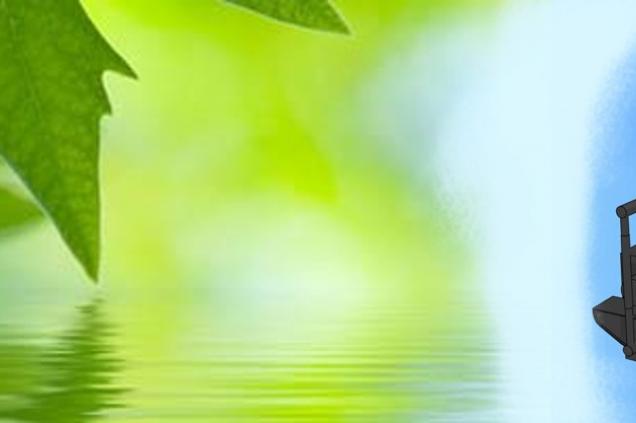
Les biomatériaux
Les biomatériaux, tels que les biopolymères, ne sont pas des produits récents. Au milieu du vingtième siècle, Henry Ford a inventé une méthode de fabrication de pièces d'automobile en plastique à...
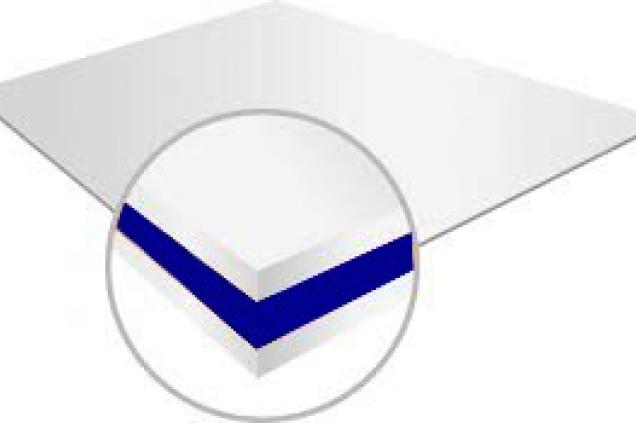
Les tôles sandwich
Le matériau sandwich multicouches comme principe de construction n'est pas nouveau (Brevet de juillet 1924).
Des applications de ce procédé se retrouvent non seulement dans la construction...
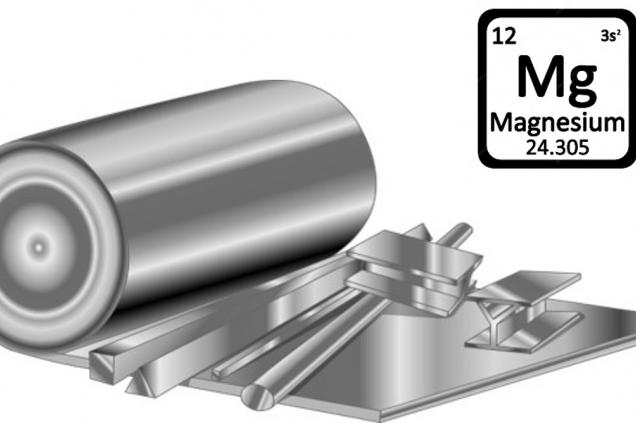
Le magnésium
Ce métal, le 4ème élément le plus abondant (après le fer, l'oxygène et le silicium) sur terre, est en progression lente mais constante dans l'industrie automobile. Il faut bien noter que la fonderie...
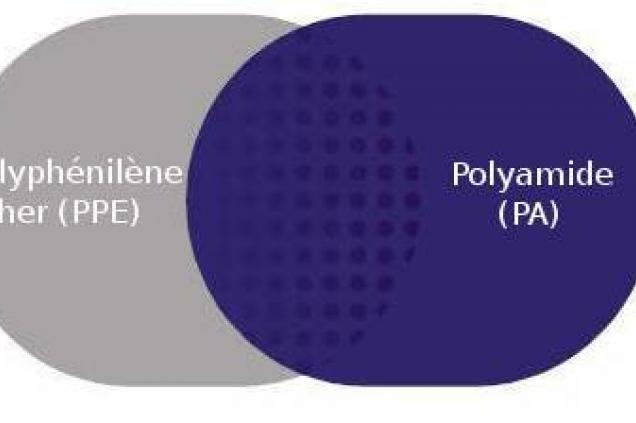
Le Noryl
En 1964, Général Electric commercialise la résine modifiée PPO Noryl et en 1988, avec la résine Noryl GTX, la société américaine offre de multiples avantages pour la conception d'ailes et autres...