- Innovation créatrice de nouvelles compétences
- Oui
- Innovation génératrice de nouvelles activités
- Oui
- Phase de développement de l'innovation
- Commercialisé depuis plusieurs années
- Date de création
- Date de mise à jour
En bref
De ses débuts hésitants dans les premières années du 19e siècle (mais aussi très riches en inventions successives de toute première importance), la sidérurgie moderne, telle que nous la connaissons aujourd'hui, naît dans les années 60 et n'a gardé que les principes de base du siècle précédent. De nos jours, il existe plus de 3000 nuances d'acier. Associé à une image de résistance et de sécurité il a très vite été incontournable dans l'industrie automobile.
L'acier a fait évoluer de façon spectaculaire les performances de l'auto (aérodynamisme, vitesse, sécurité) grâce à ses propriétés sans cesse plus étendues : capacité à former des angles arrondis, à se déformer et à absorber les chocs…. On peut aussi considérer que la recherche dans l'automobile a contribué à faire évoluer la technologie de l'acier.
Pour ces raisons, l'acier est lui aussi un élément technologique très précis, qui évolue constamment. Plus de la moitié des aciers utilisés aujourd'hui sur les véhicules n'existaient pas il y a 5 ans.
L'automobile est un parfait exemple de l'utilisation d'aciers à haute résistance avec des limites d'élasticité élevées pour fabriquer les pièces de sécurité intégrées dans la structure. Ils ont permis la réalisation d'éléments à la fois plus légers et capables de mieux absorber l'énergie d'un choc. Ils sont également plus économiques que d'autres métaux comme l'aluminium.
- Innovation créatrice de nouvelles compétences
- Oui
- Innovation génératrice de nouvelles activités
- Oui
- Phase de développement de l'innovation
- Commercialisé depuis plusieurs années
- Date de création
- Date de mise à jour

Description détaillée
A la base, l'acier est constitué principalement de fer et de carbone (jusqu'à 2,06% - au-delà de ces proportions, on parlera de fonte).
Le fer est l'un des éléments les plus abondants de la croûte terrestre (5%) et représente 35% du poids de la planète.
Du fait de son abondance, ses propriétés avantageuses (ténacité, ductilité, dureté, résilience, …), l'amélioration de ses propriétés et la possibilité d'en élargir l'éventail grâce aux traitements thermiques, sa capacité d'alliage avec de nombreux métaux pour améliorer ses caractéristiques mécaniques, ses nombreuses potentialités de mise en œuvre (mise en forme, soudabilité, …), ses capacités de recyclage, l'acier se retrouve donc être le matériau le plus utilisé dans le monde après le bois.
Dans l'automobile, il représente en moyenne, toutes sortes d'aciers confondus, 50% du poids total. Car les exigences en termes de conception imposent une grande qualité des matériaux, qui doivent être capables d'assurer le confort et la sécurité des occupants, mais également de participer à l'allégement des véhicules.

Parmi cette gamme d'aciers, c'est l'acier doux (très faible taux de carbone) qui est le plus couramment utilisé jusqu'à aujourd'hui. En fonction des véhicules et des constructeurs, il représente entre 25 et 60% de l'ensemble des aciers utilisés.
L'acier doux est très faiblement allié. Sa qualité finale sera définie tout au long du processus de fabrication, avec comme paramètres majeurs :
- La composition chimique,
- Le processus thermomécanique.
Mise en œuvre :
Les aciers doux peuvent être laminés à chaud et à froid, avec le souci permanent d'obtenir un excellent compromis entre la formabilité et le niveau de résistance attendue (la nuance métallurgique).
L'un des défauts majeurs de l'acier ordinaire est son altération par l'action de l'atmosphère, mais aussi par les divers produits avec lesquels il peut se trouver en contact, ce qui se traduit par de la rouille.
Pour protéger l'acier contre ces différentes attaques, on va le recouvrir d'un revêtement protecteur, par différent moyens :
- Électro zingage : électrodéposition d'une couche de zinc (5 à 7,5 µm / face).
- Galvanisation : défilement d'une bande d'acier dans un bain de zinc liquide (selon la demande, entre 7 et 18 µm).

Utilisation :
Les aciers doux sont destinés à la mise en forme par emboutissage profond et extra profond.

Il est utilisé massivement pour les pièces d'aspect, mais parfois également pour des pièces de structure.

Car plus sa propension à la déformation sera grande, plus il absorbera l'énergie du choc, et donc, plus la décélération subie par les occupants du véhicule sera acceptable.
Caractéristiques :
L'acier est avant tout caractérisé par ses propriétés mécaniques, définies par l'essai de traction. Ce test va définir l'aptitude du matériau à la transformation, la mise en forme par toutes les techniques modernes : emboutissage, hydroformage, etc.
Les valeurs exprimées le sont généralement en Mpa (mégapascal), ou en N/mm².
Pour un acier doux, la résistance maximale à la traction (Rm) peut aller de 250 à 400 Mpa.

Pour répondre aux exigences des constructeurs, les aciéristes ont développé des aciers à haute résistance permettant de réduire l'épaisseur des tôles sans perte de qualité et par conséquent un gain de poids important par rapport à des aciers ordinaires (30 à 40 kg d'économisés sur la seule structure du véhicule).
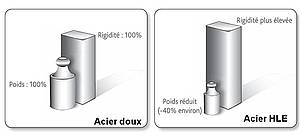
Ces aciers sont répartis en trois grandes familles :

Les aciers à Haute Limite Élastique (HLE), des aciers micro-alliés, c'est-à-dire que l'on y a incorporé, à très faible dose (environ 1%), d'autres éléments d'addition comme le carbone, le silicium, le manganèse, le phosphore, le chrome, le molybdène, le tungstène, etc.
L'élément principal de durcissement est le carbone.
Mais le silicium, le manganèse et le phosphore participent aussi à l'ajustement du niveau de résistance de l'acier.
Différents aciers HLE et leurs utilisations :
Ces différents types d'aciers HLE ont été mis au point par l'industrie de la sidérurgie afin de répondre aux différents besoins croissant des constructeurs en matière de formabilité, de résistance, de fonctionnalité.
Voici quelques exemples :
- Les aciers isotropes (300 à 400 MPa) : Pièces de peau.
- Les aciers rephosphorés (340 à 460 MPa) : Pièces de structure ou de renfort (longerons, traverses, pieds milieu, …).
- Les aciers I.F. à haute résistance (340 à 460 MPa) : Pièces complexes (passages de roue, tablier, renforts…) mais également pièces ayant un emboutissage profond (coffres, hayon, portes…).
- Les aciers Bake Hardening (300 à 480 MPa) : Pièces d'aspect et pièces de structure.
- Les aciers dispersoïdes (330 à 900 MPa) : Pièces de structure telles que liaison au sol, renforts, traverses, longerons, etc.
Les résistances des aciers HLE peuvent être comprises entre Rm = 300 et 600 Mpa (voire plus).
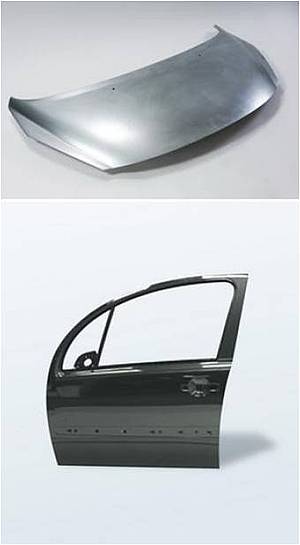

Pour la fabrication des structures automobiles, des tôles en acier de très forte résistance sont utilisées. Ces aciers à Très Haute Limite Élastique (THLE) et à Ultra Haute Limite Élastique (UHLE) ont permis la réalisation d'éléments à la fois plus légers et capables de mieux absorber l'énergie d'un choc.

En cas de choc frontal ou latéral
Sa limite d'élasticité est située entre 450 et 1500 MPa ou même plus (Méga Pascal correspond à l'équivalent en N/mm2), alors que celle d'une tôle en acier doux, qui représente la plus grande partie des aciers présents sur les véhicules actuels, est d'environ 200 MPa.
Sa haute limite d'élasticité pose des problèmes d'emboutissage, car la tôle a tendance à se comporter comme un ressort et à ne pas accepter la forme demandée. Autre inconvénient, elle supporte mal la galvanisation (traitement anticorrosion au zinc).
Plusieurs variantes peuvent exister :
- Dual phase (DP) : microstructure constituée d'une phase dure dispersée dans une base de fer plus souple qui lui confère une bonne aptitude à l'absorption de chocs et une bonne tenue à la fatigue. On l'utilise pour les pièces de structure et de sécurité telles que longeron, traverse de pare-chocs, renfort de pied de milieu, etc.
- Ferrite-bainite : mis au point pour répondre aux besoins d'allégement. Emboutis à froid, ils sont principalement utilisés dans la fabrication de pièces de structure et mécaniques.
- Aciers à phase complexe (CP) : leurs caractéristiques mécaniques et leurs résistances à la fatigue très élevées en font des aciers extrêmement bien adaptés aux tôles destinées à la résistance aux chocs ou aux pièces de liaison au sol, notamment les bras de suspension.
- Aciers TRIP : composés d'une base de ferrite souple, de parties en bainite dure et d'austénite résiduelle, ils assurent une bonne aptitude à l'absorption de chocs et disposent également d'une limite d'élasticité très élevée. Ils sont particulièrement adaptés aux pièces de structure et de sécurité.

Les aciers UHLE disposent de caractéristiques mécaniques très élevées après emboutissage à chaud.
Ils sont conçus pour être traités thermiquement puis trempés pendant l'opération d'emboutissage à chaud.
Les caractéristiques finales obtenues permettent un allégement jusqu'à 50% par rapport à une tôle HLE.
Après traitement thermique et trempe, la structure métallurgique est 100% martensitique.
Ils sont destinés aux fonctions anti-intrusion du véhicule : poutre de pare-chocs, renfort de porte, pieds milieu, montant de baie, etc.
Optimisation de la masse :
L'objectif d'obtenir un niveau de sécurité maximale sans augmenter sensiblement la masse du véhicule conduit à une utilisation importante de matériaux plus légers que l'acier ordinaire.
Des tôles THLE et UHLE incluant les aciers « multiphasés » dont la résistance augmente en fonction de la vitesse du choc, entrent ainsi à plus de 20 % dans le poids du véhicule.
Exemple :
Afin de limiter le poids du véhicule, Volvo, sur son modèle Allroad XC 90, a intégré ces différents types d'acier à hauteur de 21%.

Tous les véhicules récents sont dotés d'un côté de caisse renforcée par des ajouts matière dans la zone du pied milieu (montant central du véhicule) et par la mise en œuvre de tôle THLE/UHLE.
Ces matériaux innovants permettent au côté de caisse de se déformer progressivement et de manière importante sans rupture structurelle de la matière.
Les aciéristes proposent aux constructeurs de nouveaux produits offrant une limite avant rupture à des seuils inconnus il y a encore quelques années. Cette limite dépasse les 1300 MPa avec les aciers UHLE (Ultra Haute Limite Élastique) aussi appelés TTHLE (Très Très Haute Limite Élastique).
Ces nuances d'aciers suscitent quelques interrogations quant à leur soudabilité.
Comment les identifier ?
La documentation technique constructeur reste le moyen le plus fiable pour connaître la nature et la localisation des aciers utilisés sur le véhicule.
Diffusion sur le marché | On retrouve les différents aciers sur 100% des véhicules actuels. Leurs répartitions varient selon les marques et les modèles. |
---|---|
Constructeurs concernés | Tous les constructeurs sont concernés. |
Innovation engendrant des entretiens | Non |
Innovation engendrant des réparations | Non |
Dispositif législatif en rapport avec l'innovation | La désignation des aciers est régie par la norme NF EN 10027. Instruction technique de l'OTC IT F6. |
Contrôle technique | Les aciers seront bien évidemment soumis au regard du contrôleur technique, en tant que constituant principal de la carrosserie. |
Mots-clés | Acier doux, HLE, THLE, UHLE, Acier à haute résistance |
Méthodes et pratiques
Un élément de carrosserie en acier ne nécessite pas d'entretien ou de réparation sans qu'il ne soit endommagée par un accident de la route. Il peut dans ce cas être réparé.
Un diagnostic va permettre de déterminer l'étendue et la profondeur des dégâts afin de définir les moyens et les méthodes nécessaires à la réparation du véhicule.
Dans tous les cas, il faut toujours se référer aux préconisations du constructeur quant à la méthode de réparation à mettre en œuvre.
Pour les aciers doux et HLE,
Une remise en forme est possible, cependant, le martelage à froid modifie l'état structural du matériau. Il se forme un écrouissage (durcissement à froid), qui modifie le comportement du matériau en cas de choc (dureté = fragilité). De plus, le chauffage pour faciliter la remise en forme est proscrit.
Lors du remplacement d'un élément partiel ou d'un échange complet :
- Respecter impérativement les lignes de coupe du constructeur, afin de ne pas affaiblir la structure.

- Respecter les procédés d'assemblage thermique, ainsi que leurs caractéristiques afin de ne pas modifier le comportement général de la structure en cas de choc. Ceci impose le plus souvent l'emploi de matériel de soudage aux caractéristiques spécifiques, afin de ne pas dénaturer la tôle.
Toute intervention sur des éléments du soubassement, qui soutiennent les éléments mécaniques du véhicule, peut modifier le comportement routier du véhicule, et donc mettre en jeu la sécurité des passagers. Pour le contrôle de ces éléments, il faudra donc utiliser un banc de mesure tridimensionnel approprié.
Une remise en ligne d'un élément de structure est possible avec un vérin vecteur ou une équerre de traction.
Pour les aciers THLE et UHLE,
Le redressage de ce type d'acier, même en présence de déformations légères, n'est pas possible en raison de la haute limite apparente d'élasticité et de l'effet de retour élastique aux chocs (il se comporte comme un ressort).

Ces aciers exigent de nouvelles méthodes de réparation en cas d'intervention nécessaire du service après-vente. Une pièce endommagée doit être entièrement sectionnée et déposée, puis remplacée selon les prescriptions du constructeur.
En présence d'aciers formés à chaud et d'aciers THLE, un soudage bout-à-bout en cas de réparation va générer un affaiblissement de cette zone car ces aciers se caractérisent à la fois par un risque de fissuration à froid et un risque d'adoucissement au voisinage de la zone affectée thermiquement (ZAT).

Cet adoucissement peut, dans certaines conditions, abaisser la charge de rupture à des valeurs inférieures à celles mentionnées dans les normes.
La soudabilité des aciers à très haute limite d'élasticité (THLE/UHLE) ne va pas de soi et des risques de fissuration existent !
Les soudages MAG, MIG et tous les procédés conventionnels, y compris le brasage, peuvent être employés sans problème, dans le respect des préconisations du constructeur et des règles de savoir-faire.
Lors du soudage par points, il se crée une très petite zone influencée par la chaleur, mais du fait de la résistance accrue du matériau, une intensité de plus en plus élevée (jusqu'à 14000 A) est nécessaire au soudage.
Ceci impose le plus souvent l'emploi d'un matériel de soudage aux caractéristiques spécifiques, afin de ne pas dénaturer la tôle.
Le dépointage des tôles apparaît lui aussi plus délicat : la dureté de ces matériaux nécessite l'utilisation de forets au carbure, plus durs que le support à traiter.
Toute intervention sur des éléments du soubassement, qui soutiennent les éléments mécaniques du véhicule, peut modifier le comportement routier du véhicule, et donc mettre en jeu la sécurité des passagers.
Pour la remise en ligne, vérin vecteur et équerre doivent être adaptés à la résistance et la dureté de ces matériaux (force de traction plus élevée).
Les fiches techniques associées à ces aciers délivrent des conseils relativement limités sur leur mise en œuvre. En outre, comme il s'agit d'aciers de marque, la généralisation de conseils d'une marque à l'autre apparaît délicate.
Entreprises concernées aujourd'hui | Carrosserie / Peinture, MRA, RA2, RA1 |
---|---|
Métiers concernés | Carrossier et Peintre, Réceptionnaire |
Impact sur les compétences en atelier
- Connaître les méthodes de contrôle d'un véhicule accidenté.
- Connaître les différents aciers (caractéristiques, localisation, réparabilité…).
- Connaître les méthodes de remise en forme des différents aciers.
- Connaître les méthodes d'assemblage en carrosserie.
- Connaître les préconisations des constructeurs relatif à la corrosion.
- Savoir remettre en forme un élément en acier endommagé.
- Savoir contrôler en 3 dimensions une structure en acier endommagée.
- Savoir remettre en ligne une structure en acier.
- Savoir régler le matériel de soudure adapté (paramétrage, test d'arrachement utilisation, entretien).
- Savoir exploiter la documentation technique (endroit de coupe, méthode de remplacement…).
- Savoir remplacer un élément en acier endommagé (par soudage, collage, rivetage, vissage…).
Exemple d’outillage approprié
Pour souder ces aciers en réparation après-vente, nous avons le choix entre plusieurs types de postes à souder :
1. Les semi-automatiques MAG sous protection gazeuse (argon+CO2).

Poste MAG standard

Poste MAG pulsé synergique
À titre indicatif, quelques combinaisons fil / gaz préconisées pour le soudage MAG des aciers :
- Ferrite-bainite :
- Fil d'apport de type GS2 ;
- Gaz de protection ATAL 5 ou ATAL 18.
- TRIP :
- Fil d'apport de type G3Si1 ;
- Gaz de protection argon + 8 % de CO2.
2. Les soudeuses par point à contrôle de courant constant, refroidissement liquide et traçabilité du travail effectué.

Pourquoi ce type d'outillage ?
Le soudage par points consiste à enserrer entre deux électrodes les tôles à souder, puis de leur faire subir un courant électrique de forte intensité mais bref. La chaleur engendrée par ce courant fait fondre localement le métal, ce qui crée, après solidification, un point de soudure. On parle aussi de soudage électrique par résistance.
Une soudure par points est réalisée en une à deux secondes, avec un temps effectif de passage du courant de quelques dixièmes de seconde. Les aciers à haute résistance peuvent perdre leurs propriétés spécifiques de résistance aux chocs à cause de la chaleur ajoutée pendant le soudage. Il est donc primordial de limiter au maximum l'apport thermique pendant l'opération. Lors du soudage par points, il se crée une très petite zone influencée par la chaleur, ce qui n'affecte pas la microstructure de la tôle.
À lire aussi dans la même section
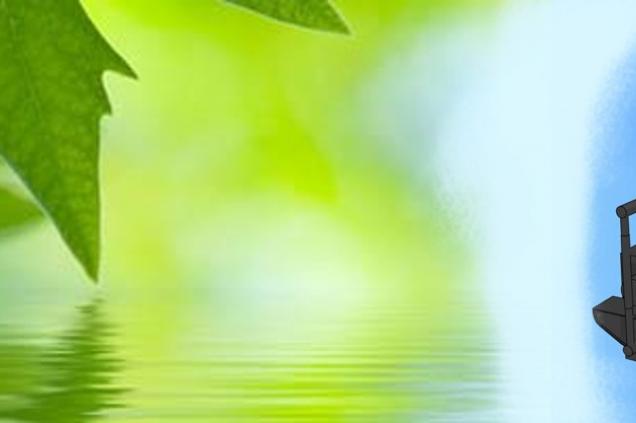
Les biomatériaux
Les biomatériaux, tels que les biopolymères, ne sont pas des produits récents. Au milieu du vingtième siècle, Henry Ford a inventé une méthode de fabrication de pièces d'automobile en plastique à...
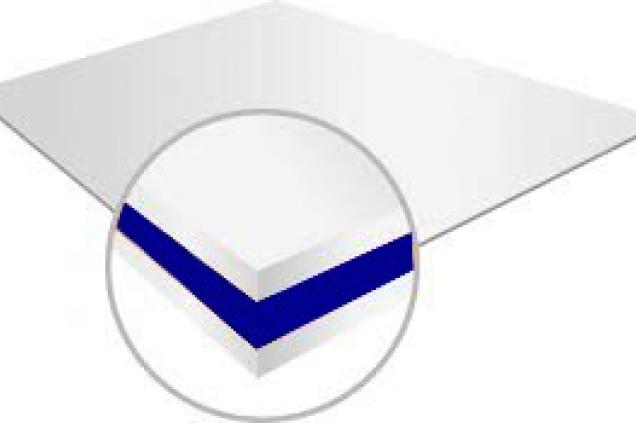
Les tôles sandwich
Le matériau sandwich multicouches comme principe de construction n'est pas nouveau (Brevet de juillet 1924).
Des applications de ce procédé se retrouvent non seulement dans la construction...
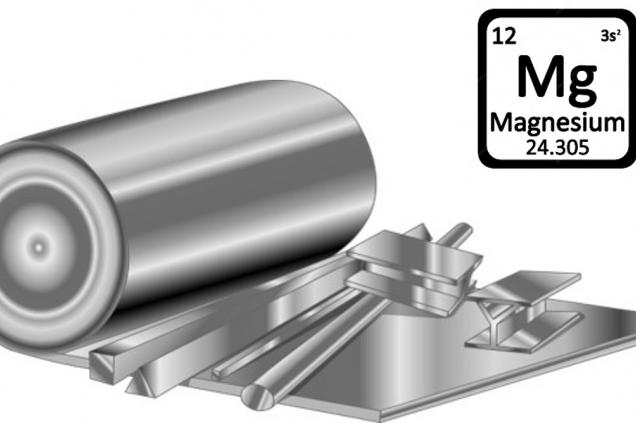
Le magnésium
Ce métal, le 4ème élément le plus abondant (après le fer, l'oxygène et le silicium) sur terre, est en progression lente mais constante dans l'industrie automobile. Il faut bien noter que la fonderie...
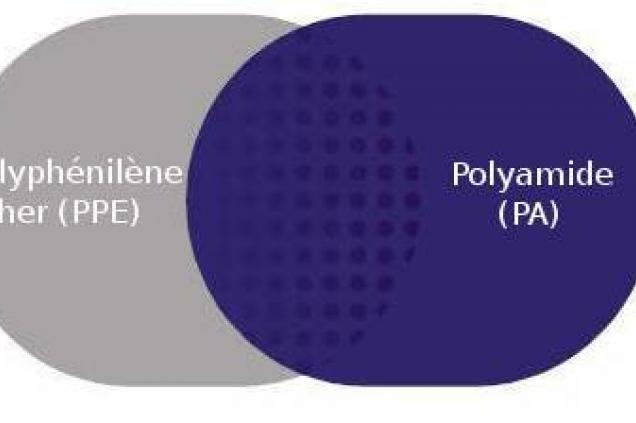
Le Noryl
En 1964, Général Electric commercialise la résine modifiée PPO Noryl et en 1988, avec la résine Noryl GTX, la société américaine offre de multiples avantages pour la conception d'ailes et autres...