- Innovation créatrice de nouvelles compétences
- Oui
- Innovation génératrice de nouvelles activités
- Oui
- Phase de développement de l'innovation
- Commercialisé depuis plusieurs années
- Date de création
- Date de mise à jour
En bref
L'histoire de ce matériau remonte à la fin du 19e siècle et les choses ont très peu changé jusqu'en 1961, lorsque la fibre a commencé à être fabriquée à partir de polyacrylonitrile (PAN) par Shindo au Japon. Cette avancée a marqué le début des matériaux en fibre de carbone de « haute performance ».
Repoussant toujours les limites, le matériau a également fait ses débuts en Formule 1 en 1981 avec McLaren et est devenu depuis un élément essentiel du monde de la course automobile.
Dans l'industrie automobile, le matériau commence enfin à apparaître sur le marché des automobiles de performance haut de gamme. Des pare-chocs avant et arrière, un capot, un toit, des poutres et même des structures entières sont produits en plastique renforcé de fibre de carbone.
Malgré tout, les besoins d'allègement vont rendre ce matériau plus populaire et certains constructeurs ont déjà dépassé cet usage très restreint. Le constructeur allemand BMW commercialise depuis 2013, deux véhicules, i3 (électrique) et i8 (hybride), de moyenne série ayant recourt massivement au PRFC. Alfa Roméo avec sa petite sportive made in Italie, la 4C, avec une structure en fibre de carbone et Ford a dévoilé un capot renforcé de fibres de carbone monté dans un premier temps sur la Focus. Audi vient de rajouter une paroi en PRFC, pour rigidifier sa structure, entre l'habitacle et le coffre de son vaisseau amiral A8 pourtant la référence du tout alu.
- Innovation créatrice de nouvelles compétences
- Oui
- Innovation génératrice de nouvelles activités
- Oui
- Phase de développement de l'innovation
- Commercialisé depuis plusieurs années
- Date de création
- Date de mise à jour

Description détaillée
La fibre de carbone, communément carbone, fait partie d'une famille de matériaux appelés « composites ». Il s'agit d'une combinaison de deux ou plusieurs matériaux, des fibres de carbone et une résine. Lorsque la résine est durcie, les fibres de carbone renforcent le matériau, mais les constituants demeurent séparés et distincts tout en formant un seul composant, du plastique à renfort de fibre de carbone (PRFC). Autrement dit, les produits ne subissent pas de réaction chimique, mais demeurent deux entités chimiques séparées. Les matériaux composites les plus primitifs sont la paille et la boue utilisées pour la fabrication de briques pour la construction de bâtiments. Plus moderne et plus connu, la fibre de verre constitue un autre exemple de ce type de matériau.

La résistance du matériau vient de la bonne concentration de la résine, de la quantité de fibres de carbone et de leurs orientations ou de la forme de tissage.
Les matériaux constitutifs sont classés en deux catégories :
- Le renforcement est une fibre robuste (telle que la fibre de carbone) qui donne au matériau sa résistance à la traction.
- La matrice, généralement une résine polymère ou époxyde. Cette résine plastique agit comme un adhésif afin de lier les fibres ensemble. Elle aide également le matériau composite à résister à la dégradation et protège les fibres de l'environnement.
La combinaison de ces éléments lui confère des propriétés que n'offrent aucun matériau naturel.
À l'origine, la fibre de carbone est une fibre textile en polyacrylonitrile (PAN) soumise à différentes températures et pressions. Les paquets de fibres sont ensuite assemblés en toiles non tissées avant de recevoir une injection de résine qui les solidifie et les transforme en plastique à renfort de fibre de carbone (PRFC). Ce processus n'est pas entièrement automatisé et requiert beaucoup d'énergie.
En fonction de la forme, de la fonction et des exigences opérationnelles de chaque composant, on peut utiliser l'une des trois techniques de fabrication :
- Carbone forgé : ici, des matériaux sont thermos comprimés avec des fibres de carbone courtes dans un moule. Ce processus facilite la réalisation de structures complexes et a été utilisé pour des pièces comme le fond du châssis monocoque ou les bras de suspension.

- Pré-imprégné : des couches de fibres de carbone sont imprégnées d'une résine liquide thermodurcissable. Elles sont pressées dans des moules et cuites sous pression dans un four. Les composants en « pré-imprégné » présentent une excellente finition de surface, raison pour laquelle cette technique est la plus utilisée pour réaliser les parties visibles.

- Braiding : il s'agit d'une méthode de fabrication de matériaux composites qui provient du secteur textile. Braid est en fait une composition textile réalisée grâce au croisement de fils disposés horizontalement et en diagonale.

Le carbone est généralement considéré comme le plus robuste qu'on connaisse et possède un rapport résistance/poids incomparable, aussi solide que l'acier, mais avec la moitié de son poids.
Comparons une même pièce fabriquée dans trois matériaux différents :

Sa longévité est également un avantage puisqu'il ne connaît pas de problèmes d'allongement, de fluage, de fatigue, de pliage, de faiblesse ou de corrosion avec le temps.
De plus, il peut être enroulé, tressé, enveloppé, stratifié ou taillé de façon unique afin de répondre aux exigences de sécurité et de performance.
La fibre de carbone est aussi un conducteur d'électricité, contrairement à la plupart des fibres de renforcement.
Enfin, elle n'est pas sensible aux variations de température, ne se dilate pas et ne se contracte pas.
Dans une industrie sans cesse à la recherche du moindre gain de poids, tous ces avantages pourraient nous faire croire qu'il s'agit du matériau idéal. Mais certains inconvénients, et non des moindres, freinent son développement.
Tout d'abord son prix, un élément de carrosserie en fibre de carbone coûte cinquante fois plus cher que le même en acier et de plus, contrairement à ce qu'on croit, il a une tenue aux chocs et à l'abrasion limitée.
Et, les éléments en fibre de carbone de fabrication classique sont impossibles à valoriser en fin de vie, finissant au mieux dans l'asphalte de nos routes après avoir été découpés en petits morceaux. En revanche, les fibres courtes constituant les pièces en carbone forgé peuvent être recyclées après une opération de pyrolyse permettant de brûler la résine leur servant de matrice. Après ré-imprégnation, les fibres ainsi récupérées sont alors réutilisables pour la fabrication de pièces aux propriétés mécaniques très proches des éléments originels. Une caractéristique essentielle pour satisfaire aux normes exigibles depuis 2015 imposant de pouvoir recycler/valoriser 95 % de la masse de tout nouveau véhicule mis sur le marché.
Depuis quelques années, elle a gagné en popularité et n'est plus l'exclusivité des entreprises à gros budget. La recherche incessante de réduction de poids dans l'automobile est sans aucun doute la raison de cet intérêt soudain pour ce matériau mythique.
Pour les petites séries, la fabrication reposait sur un tissu pré-imprégné de résine mis en forme artisanalement sur un moule, puis chauffé dans un four autoclave. Mais pour rendre possible l'utilisation de ce matériau en série plus importante, un changement de procédé de fabrication des pièces était nécessaire. Les allemands BMW et SGL Carbon, ont mis au point une déclinaison du procédé RTM (Resin Transfer Moulding) utilisé dans l'aéronautique, qui utilise un tissu de fibres de carbone « sec ». Le tissu transite par des moules chauffants où la résine est injectée et polymérisée. La fabrication d'une pièce, automatisée, ne prend que quelques minutes, contre plusieurs jours avec la méthode traditionnelle.

Grâce au procédé RTM, la fabrication de pièces de carrosserie en plastique à renfort de fibre de carbone devient automatisable et donc compatible avec la production en série.
Le procédé développé par Lamborghini prévoit l'utilisation d'un matériau composé de fibres courtes omnidirectionnelles pré-imprégnées d'une résine thermoplastique. Les pièces sont forgées en quelques dizaines de secondes sous 60 bars de pression et une température de 120°C. Elles sont ainsi beaucoup plus simples à concevoir que celles fabriquées selon le procédé traditionnel, mais surtout, elles sont véritablement recyclables.

Ces procédés de fabrication inédits ont rendu la construction en fibre de carbone beaucoup plus abordable, rapide et facilement automatisable. Son champ d'application va progressivement s'élargir, jusqu'à l'automobile de grande production. L'allégement devient en effet une impérieuse nécessité pour satisfaire les objectifs de réduction d'émission de CO2.
Même si l'utilisation du plastique renforcé de fibre de carbone en grande série et sur la voiture de monsieur tout le monde n'est pas encore envisageable dans l'immédiat, les constructeurs s'efforcent à trouver des solutions innovantes qui s'en approchent pas à pas.
Diffusion sur le marché | Jusqu'à présent, cette matière noble était réservée au domaine du sport automobile et à quelques super-cars, néanmoins elle remplace progressivement l'acier pour certaines pièces de carrosserie.
|
---|---|
Constructeurs concernés | Bugatti, Pagani et Koenigsegg (supercars).<br />BMW, Porsche, Mercedes, Lamborghini et Audi, Ferrari, Alfa Roméo, Aston Martin,<br />Toyota (Lexus), les américains General Motors et Ford, pour des modèles produits en faible quantité. |
Innovation engendrant des entretiens | Non |
Innovation engendrant des réparations | Non |
Dispositif législatif en rapport avec l'innovation | Pour la production ou la réparation, c'est la directive européenne n° 1999/13 du 11 mars 1999 relative à la réduction des émissions de composés organiques volatils. |
Contrôle technique | La fibre de carbone n'entre dans le champ d'application du contrôle technique qu'au travers de la nature de la pièce qu'elle compose. Une pièce réalisée en fibre de carbone doit satisfaire aux mêmes obligations qu'une pièce en alu ou en acier. Elle présente cependant l'avantage de ne pas être sensible à la corrosion. |
Mots-clés | Fibre de carbone, carbone, plastique renforcé de fibre de carbone (PRFC) |
Méthodes et pratiques
Le plastique renforcé de fibre de carbone est un matériau très stable qui ne nécessite ni entretien, ni réparation sans qu'il ne soit endommagé par un accident de la route. Le matériau offre quelques possibilités de réparation collision, mais les recommandations du fabricant du véhicule doivent être suivies. À noter que certains fabricants de colle ont, eux aussi, élaboré des procédures de réparation. Lorsqu'il est moulé dans la forme, le mélange de résine et de carbone est considéré comme le lien principal et c'est dans cet état que le lien sera le plus fort. Toute réparation est considérée comme liaison secondaire, ce qui signifie que l'intégrité de la réparation dépend des propriétés adhésives des résines. Les pièces structurelles endommagées sont généralement remplacées car il n'existe aucun moyen de garantir que la pièce réparée aurait la même solidité que la pièce d'origine.
Un problème connexe est la difficulté de détecter les bris, car le plastique renforcé de fibre de carbone peut absorber un choc et sembler intact, mais en réalité présenter un bris interne extrêmement difficile à détecter. Essentiellement, la science permettant de déterminer les défauts des matériaux composites demeure assez primitive. On peut procéder à un examen attentif avec une lumière vive en recherchant le délaminage dans certains cas, mais cette méthode n'est pas infaillible. Une approche plus sophistiquée utilise les ultrasons afin de capter les échos doubles signifiant le délaminage. Les ultrasons sont assez directs sur une surface plate, mais au niveau des articulations, qui constituent habituellement les zones critiques, les couches de fibre confondues donnent logiquement des échos confondus. Les ingénieurs peuvent alors comparer les nouveaux résultats des ultrasons aux résultats précédents en recherchant les différences entre les échos signalant le délaminage.

Mais lorsque l'on a détecté une fêlure, et que certaines fibres sont cassées, on ne peut pas pour autant réparer facilement le plastique renforcé de fibre de carbone. Du fait de sa structure faite de millions de fibres extrêmement fines qui sont enroulées pour former un fil, le tout agglutiné dans une résine durcie, il est impossible de les séparer pour les remplacer. Il faut donc soit découper autour de la zone abîmée et remplir couche mince sur couche mince en faisant attention à bien homogénéiser, dans la mesure du possible, tout en sachant qu'une parfaite homogénéité est impossible et donc que le matériau après cette opération sera fragilisé, soit remplacer la pièce.
Enfin, étant donné sa composition en carbone, le plastique renforcé de fibre de carbone ne doit pas être exposé aux flammes et le perçage coupe la fibre qui donne sa résistance au matériau. C'est pour cette raison que les composants sont généralement collés et non vissés en place.
Il faudra donc mettre en œuvre le procédé de collage spécifique et suivre les recommandations des fiches techniques du produit.
Malgré tout, certains constructeurs autorisent la réparation des éléments de peau utilisés à des fins esthétiques, comme les pare-chocs avant, à condition que les dégâts ne s'étendent pas jusqu'à un bord. Les cassures ou les déchirures doivent être réparées sur les deux faces.
Cette réparation s'effectue en pyramide pour augmenter au maximum la surface d'adhésion des matériaux de réparation. Les bords ou les angles vifs doivent être arrondis et un large chanfrein doit être fait autour de la réparation.

Un renfort doit être placé sur la partie intérieure, par exemple à partir d'un morceau de PRFC, mais si vous n'avez pas de morceau de composite pour le renfort, vous pouvez en fabriquer un avec la toile et la résine de réparation. Sur la partie extérieure, appliquez des couches successives en pyramide, du plus petit au plus grand progressivement, jusqu'à ce que le chanfrein soit rempli.

À l'aide d'un rouleau, chassez l'air et séchez la réparation par une source de chaleur. Après séchage, poncez et effectuez les opérations de finition.
Entreprises concernées aujourd'hui | Carrosserie / Peinture, Spécialistes |
---|---|
Métiers concernés | Carrossier et Peintre, Réceptionnaire |
Impact sur les compétences en atelier
- Connaître de l'outil informatique pour la lecture de documentation.
- Connaître des matériaux composites (fabrication, comportement aux chocs, réparabilité, …).
- Savoir mettre en œuvre les techniques de réparation et de peinture des composites.
- Savoir mettre en œuvre les techniques de collage.
- Savoir remplacer un élément amovible.
Exemple d’outillage approprié
Kit de réparation rapide :
Résine époxy et son durcisseur, toile de fibre de carbone, matériel d'application et de protection.

À lire aussi dans la même section
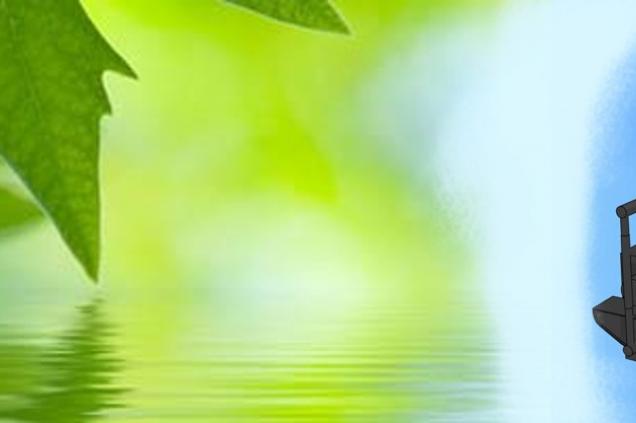
Les biomatériaux
Les biomatériaux, tels que les biopolymères, ne sont pas des produits récents. Au milieu du vingtième siècle, Henry Ford a inventé une méthode de fabrication de pièces d'automobile en plastique à...
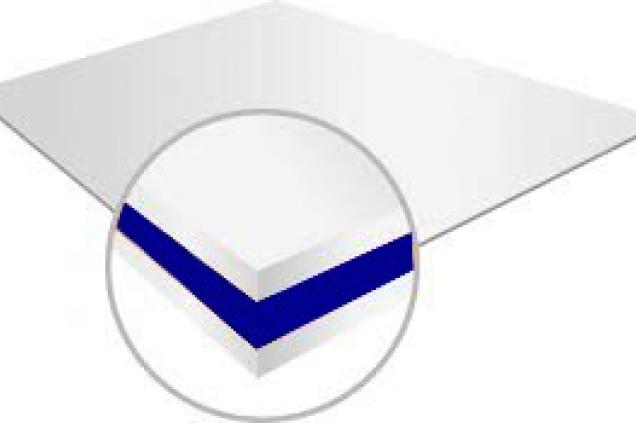
Les tôles sandwich
Le matériau sandwich multicouches comme principe de construction n'est pas nouveau (Brevet de juillet 1924).
Des applications de ce procédé se retrouvent non seulement dans la construction...
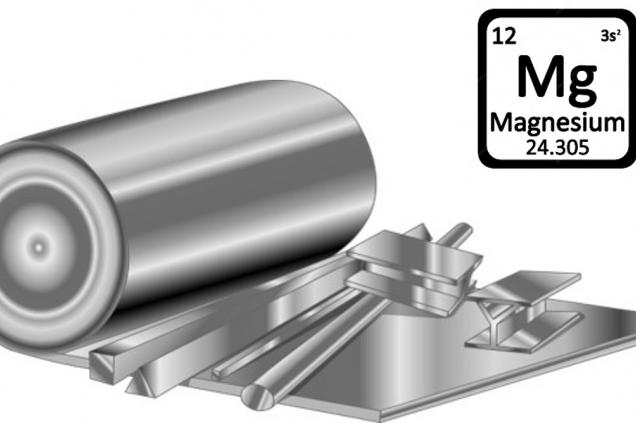
Le magnésium
Ce métal, le 4ème élément le plus abondant (après le fer, l'oxygène et le silicium) sur terre, est en progression lente mais constante dans l'industrie automobile. Il faut bien noter que la fonderie...
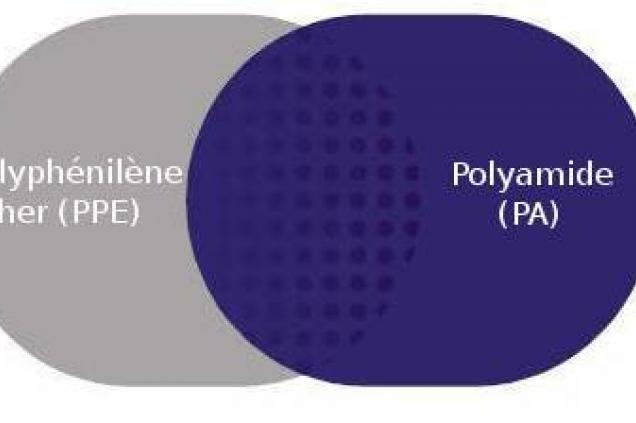
Le Noryl
En 1964, Général Electric commercialise la résine modifiée PPO Noryl et en 1988, avec la résine Noryl GTX, la société américaine offre de multiples avantages pour la conception d'ailes et autres...