- Innovation créatrice de nouvelles compétences
- Oui
- Innovation génératrice de nouvelles activités
- Oui
- Phase de développement de l'innovation
- Commercialisé depuis plusieurs années
- Date de création
- Date de mise à jour
En bref
La notion des voitures légères à l'aide des matériaux innovateurs ne date pas d'aujourd'hui et bien qu'on ne puisse pas parler de véritable structure, la première utilisation de l'aluminium dans l'automobile fût la « Jamais-Contente » du belge Camille Jenatzy en 1899. De nombreux autres exemples au fil du temps, cependant, cette évolution fut éphémère parce que plus chère qu'une solution classique en acier et l'allégement des automobiles n'était pas un objectif prioritaire.
Plus récemment et après de multiple tentative, le Space Frame d'Audi voit le jour déguisé en A8 et présenté au salon de Frankfort à l'automne 1993. Suivit par la XJ de Jaguar, première voiture de série à comporter une structure de carrosserie monocoque fabriquée en tôle d'aluminium et issu du même fournisseur Alcan Inc.
Aujourd'hui, les perspectives de développement de l'aluminium dans la carrosserie automobile se précisent. Ce regain d'intérêt s'explique par les nouvelles orientations qui s'imposent à l'automobile (règlementation sur la réduction des émissions de CO2). L'objectif majeur des constructeurs pour le futur est de réduire la masse de leur carrosserie.
On pourrait gagner dans l'absolu 150 kg avec des alliages d'aluminium, mais ce ne sera pas le cas pour des raisons liées au coût et de contraintes diverses. La voiture de demain sera multi matériaux et l'aluminium en fera partie.
- Innovation créatrice de nouvelles compétences
- Oui
- Innovation génératrice de nouvelles activités
- Oui
- Phase de développement de l'innovation
- Commercialisé depuis plusieurs années
- Date de création
- Date de mise à jour

Description détaillée
Les structures en aluminium se distinguent par deux concepts de fabrication différents :
- Le « Space Frame » qui consiste à faire un châssis en aluminium de diverses épaisseurs à l'aide de tubes extrudés (en bleu sur l'illustration) dont chaque extrémité est jointe de manière très complexe avec des pièces de liaison (en rouge) sous forme de nœuds moulés à haute pression et auquel on rajoute des tôles d'aluminium à haute résistance (en vert). Adopté par Audi, par exemple.

- La « monocoque en aluminium » qui est une structure fabriquée d'un seul tenant dont la grande particularité technique provient du fait qu'elle soit principalement collée/rivetée. Cette technologie a été introduite par Jaguar sur ses modèles XJ et XK.

Pourquoi l'aluminium ?
Les carrosseries en aluminium sont reconnues d'abord pour leur légèreté. Par exemple, une Audi A8 est environ 40 % plus légère (120 à 140 kg) qu'une voiture comparable dotée d'une carrosserie en acier classique.
Cette réduction de poids a pour autre avantage la réduction de la consommation en carburant, des émissions de CO2 et donc de l'impact environnemental.

Même si la fabrication des pièces en aluminium provoque une émission supplémentaire de CO2 de 100 kg par rapport à la fabrication des pièces en acier. Cette augmentation de l'impact sur l'environnement est compensée plusieurs fois par la diminution de la consommation d'essence, ce qui équivaut à une réduction des émissions de CO2 d'approximativement 1500 kg sur toute la durée de vie de la voiture.
Une voiture plus légère comporte de multiples avantages : une économie de carburant, on l'a vu, mais aussi de meilleures accélérations et une distance de freinage plus courte.
Malgré sa légèreté, l'aluminium possède une excellente robustesse, car il est d'une grande rigidité face aux efforts de torsion (supérieure de 60% par rapport à l'acier), spécialement pour la fabrication de pièces composées de plusieurs cellules en aluminium extrudé. En effet, une pièce extrudée multicellulaire avec des renforts intérieurs à même la pièce améliore grandement la rigidité et la robustesse. Cela peut contribuer à une stabilité accrue dans les virages serrés et à une meilleure répartition de la motricité sur le pavé.
Une des principales raisons qui justifie l'utilisation de l'aluminium sur les véhicules à hautes performances est le facteur sécurité. Ces voitures sont conçues pour rouler à des vitesses plus élevées, ce qui peut entraîner des forces d'impacts plus grandes et des dommages plus sévères.
Les réactions de ce métal à la suite d'une collision sont très prévisibles, ce qui permet de concevoir des véhicules qui absorbent bien l'énergie et la dirigent loin des occupants.

Les avantages de l'aluminium ne se résument pas à la légèreté et à la haute rigidité de la carrosserie. Ce métal est de plus très malléable, a une excellente résistance à la corrosion, il est 100 % recyclable et il permet une liberté de formage, de pièces moulées et de profilés complexes impossible avec les tôles d'acier.
Des innovations lancées année après année :
- Réduction du nombre de composants de la carrosserie.
- Pièces coulées multifonctionnelles de grande taille utilisées au niveau des fixations des suspensions et de la ligne de transmission réalisées dans des matériaux plus robustes permettant de réduire de 20 % l'épaisseur des parois.
- Perfectionnement de la technologie aluminium, avec :
- Des cordons de soudure laser.
- Des profilés du cadre de pavillon réalisés par hydroformage.
- Des nouveaux alliages d'aluminium hautement résistants faisant leur apparition en certains points clés de la structure, dans le but d'améliorer sa rigidité et sa durabilité tout en réduisant la quantité de matière utilisée.
- Un alliage « Fusion », sorte de « sandwich » d'aluminium hautement résistant qui permet de réduire l'épaisseur des panneaux de carrosserie de 10 %, est utilisé au niveau des ailes, des panneaux de toit et du couvercle de coffre.
- Évolution de la conception avec une structure optimisée :
- Réduire le nombre de joints et éliminer les assemblages complexes.
- Emboutir un panneau latéral d'un seul tenant.
- Simplifier les processus de production, moins de rivets et moins d'adhésif.
- Réduire la consommation d'énergie à la fabrication.
On a repoussé les limites de construction automobile avec ces concepts
A l'aide de techniques empruntées à l'industrie aérospatiale, ce type de structure présente des avantages décisifs par rapport à une carrosserie en acier conventionnelle : accélérations plus vives, comportement plus précis, distances de décélération plus courtes, sécurité accrue et consommation plus basse.
Cependant leurs fabrications restent très coûteuses et leurs utilisations restent restreintes.

Pour une Audi R8, par exemple, la carrosserie est en grande partie assemblée à la main. Des spécialistes hautement qualifiés produisent 99 mètres de soudure pour relier les pièces moulées et profilées. Les panneaux métalliques dans la structure sont reliés par 782 rivets auto poinçonneurs et 308 vis Flowdrill automatiquement définies.


Un total de 38 machines à souder, cinq séries de pinces à riveter et seulement cinq robots sont utilisés dans l'atelier de carrosserie. Ces derniers pour les processus où un niveau particulier de force est nécessaire.

L'innovation sur les structures en aluminium vient en grande partie aussi de l'évolution des techniques d'assemblage.
Diffusion sur le marché | Le coût de fabrication de ce type de structure limite son utilisation aux véhicules de très haut de gamme. |
---|---|
Constructeurs concernés | Space Frame : Audi (A2, A8, R8), BMW (Z8), Ferrari (Modena), Maserati (Grantourismo), Mercedes (SLS-AMG), Alpine (A110), Corvette (ZO6), Aston Martin (Vanquish)<br />Monocoque : Jaguar, Honda, Lotus |
Innovation engendrant des entretiens | Non |
Innovation engendrant des réparations | Non |
Dispositif législatif en rapport avec l'innovation | La responsabilité du carrossier en réparation automobile est de respecter les règles de l'art telles que définies par la Norme Française NF X 50-210 de 1992 et de tenir compte des évolutions technologiques. Instruction techniques |
Contrôle technique | Ces véhicules doivent être réparés en respectant de sévères normes constructeurs, ce qui implique d'être très attentif pour tous les véhicules qui présentent des traces de réparations. |
Mots-clés | Space Frame, ASF, structure en aluminium, monocoque |
Méthodes et pratiques
La structure de carrosserie en aluminium ne nécessite pas d'entretien ou de réparation sans qu'elle ne soit endommagée par un accident de la route. Elle peut dans ce cas être réparé. L'inspection minutieuse de chaque section du véhicule est impérative dès le début du processus d'évaluation, car les coûts de réparation peuvent grimper très rapidement. En général, on peut affirmer que, dès qu'un élément de la structure a subi des dommages apparents, il est préférable de le remplacer.
Les échelonnements de rigidité dans les zones de la carrosserie menacées en cas d'accident ont pour but de réduire la pénétration du dommage et les frais de réparation s'y rapportant. La conception de l'avant et à l'arrière de certain véhicule suit ce principe et l'un des concepts de réparation est le remplacement de pièces vissées. Il convient de souligner que la majeure partie des accidents de la route sont relativement mineures. Sur ce type de véhicule, tous dommages subis à une vitesse d'impact allant jusqu'à 15 km / h peuvent être réparées sans avoir besoin de travaux de soudage.
Si un gros travail de réparation devrait néanmoins être nécessaire, des ateliers spécialisés parfaitement équipés pour corriger les dégâts sont nécessaires.
Analyse des dommages
Lors de l'évaluation des dommages et avant de commencer les réparations, il faut connaître les caractéristiques de l'aluminium et de ses différents alliages et en tenir compte. En effet, la rigidité de l'aluminium augmente lorsqu'il est formé à l'usine par des procédés comme l'embossage, le pliage ou l'estampillage, qui renforcent le lien entre les molécules internes. Toute tentative subséquente de le plier ou déplier, ou de le former à nouveau, accroît sa résistance et le rend friable.
Lors du contrôle des pièces endommagées, il faut vérifier avec soin l'état des cordons de soudure et des pièces coulées et rechercher les fissures éventuelles. Celui-ci s'effectue par pénétration d'un agent de coloration.

1.Nettoyage de la fissure
2.Application du produit de contraste
3.Retrait de l'excédent de produit
4.Application de la substance révélatrice
Identifier l'aluminium
Pour identifier quelles composantes sur une voiture sont fabriquées en aluminium, on peut utiliser un aimant ou se référer au manuel du constructeur. Comme il existe plusieurs types d'alliages en aluminium (de 1000 à 7000 par incréments de 1000) et que certains aluminiums peuvent être chauffés alors que d'autres pas, il est impératif de savoir de quelle catégorie il s'agit. Toutes ces informations sont normalement disponibles sur la documentation technique du constructeur.
Réparer ou remplacer
Afin de conserver l'intégrité structurale et la sécurité primaire de la voiture, il est souvent préférable de simplement remplacer les composantes et les panneaux en aluminium endommagés. S'ils sont réparables, la méthode suggérée est de débosseler de l'intérieur vers l'extérieur. Selon qu'un panneau est riveté ou boulonné, il est plus facile de décider s'il sera réparé ou remplacé à cause du temps de main-d'œuvre consacré.
Les profilés extrudés doivent être remplacés en cas d'endommagement. Le redressage n'est pas contrôlable à ce niveau. Le remplacement s'effectue par sections suivant la nature de l'endommagement et moyennant l'utilisation de manchons dans la zone de découpe ou bien concerne la totalité de la pièce. Les profilés et sections de profilés remplacés sont assemblés par soudage sous gaz de protection (MIG).


Les pièces coulées endommagées doivent être remplacer systématiquement, car pour des raisons de résistance il n'est pas autorisé de redresser ces pièces. Du fait de rigidité élevée, on court le risque de formation de fissures. Les méthodes d'assemblage utilisées sont le soudage sous gaz de protection (MIG), le rivetage et le collage.
Utilisation de la chaleur
Si le type d'aluminium à réparer peut-être chauffé, il faut s'assurer de conserver la température du métal à l'intérieur des paramètres permis en utilisant un thermomètre à rayons infrarouges et être certain que cette zone ne comporte aucun enduit d'assemblage adhésif. L'utilisation de la chaleur permet aux molécules de « se détendre » et facilite le redressage des pièces simples.

Notez que pour certaines réparations, un pistolet à chaleur peut être suffisant. Il faut s'assurer de bien contrôler la dissipation de la chaleur, car le taux de conductivité de ce métal est très élevé. Les sections d'aluminium déchirées ou craquées ont probablement subi un stress excessif dû à un impact ou au déplacement de composantes adjacentes. À ce moment, la plupart des constructeurs recommandent de remplacer au lieu de réparer.
Danger de contamination
À cause du danger de corrosion galvanique, il faut à tout prix isoler les véhicules et composantes en aluminium des autres en acier ou tout autre métal à cause des risques de contamination, et les outils de réparation employés ne doivent pas être utilisés pour d'autres voitures dont la carrosserie est en acier.
Entreprises concernées aujourd'hui | Carrosserie / Peinture, MRA, RA2, RA1 |
---|---|
Métiers concernés | Carrossier et Peintre, Réceptionnaire |
Impact sur les compétences en atelier
- Connaître les méthodes de diagnostic d'un véhicule accidenté
- Connaître les différents alliages d'aluminium (caractéristiques, composition, localisation…)
- Connaître les méthodes d'assemblage d'une structure en aluminium
- Connaître les méthodes de redressage de l'aluminium
- Savoir réaliser un diagnostic d'un véhicule accidenté
- Savoir souder l'aluminium (soudure MIG)
- Savoir utiliser les différents outillages préconisés (riveteuse, …)
- Savoir utiliser les produits de collage
- Savoir remettre en forme un élément en aluminium
- Savoir refaire les traitements de surface sur l'aluminium
Exemple d’outillage approprié
Pistolet à colle bi-composant

Pince à rivet auto-poinçonneur

À lire aussi dans la même section
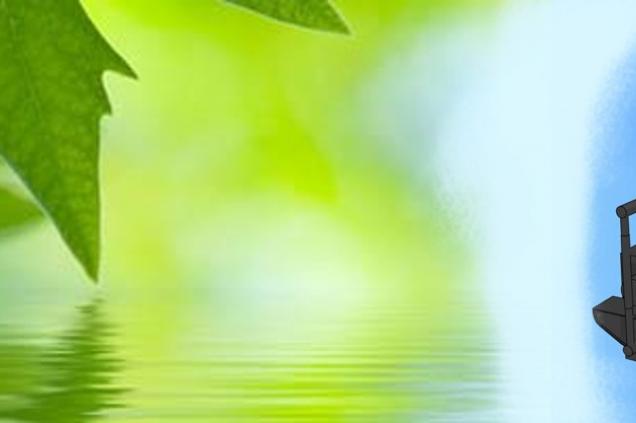
Les biomatériaux
Les biomatériaux, tels que les biopolymères, ne sont pas des produits récents. Au milieu du vingtième siècle, Henry Ford a inventé une méthode de fabrication de pièces d'automobile en plastique à...
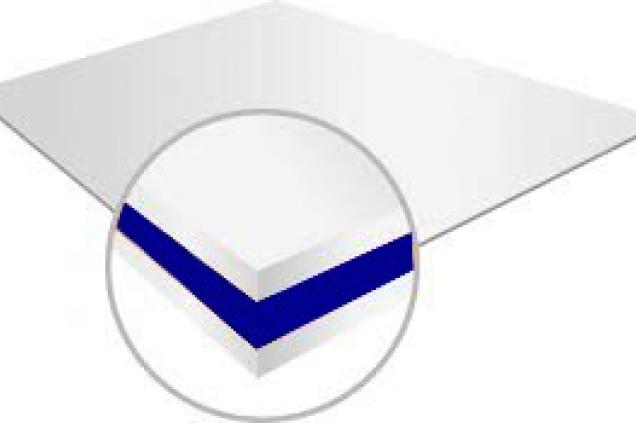
Les tôles sandwich
Le matériau sandwich multicouches comme principe de construction n'est pas nouveau (Brevet de juillet 1924).
Des applications de ce procédé se retrouvent non seulement dans la construction...
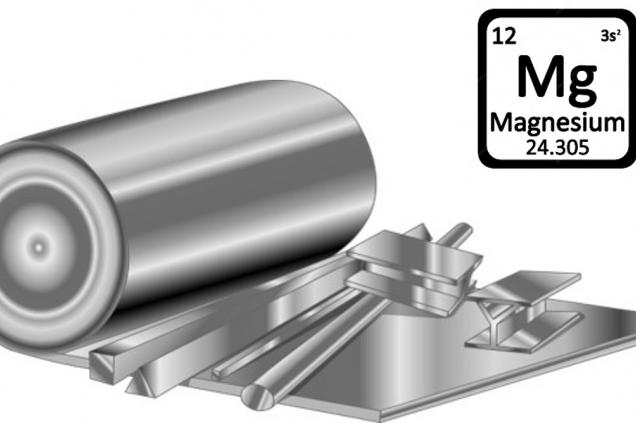
Le magnésium
Ce métal, le 4ème élément le plus abondant (après le fer, l'oxygène et le silicium) sur terre, est en progression lente mais constante dans l'industrie automobile. Il faut bien noter que la fonderie...
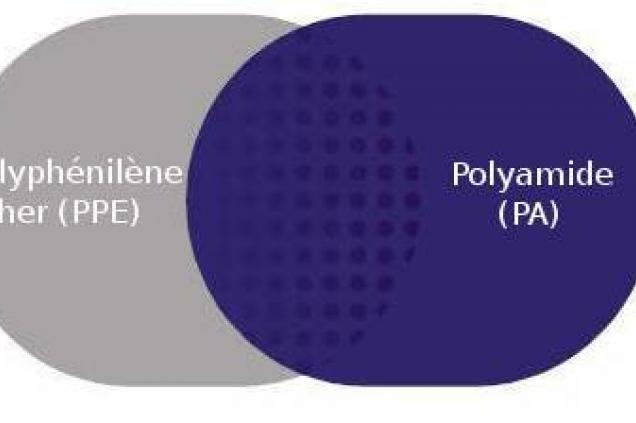
Le Noryl
En 1964, Général Electric commercialise la résine modifiée PPO Noryl et en 1988, avec la résine Noryl GTX, la société américaine offre de multiples avantages pour la conception d'ailes et autres...